AUCO Raised Floor Systems
AUCO Raised Floor Systems are of great importance in ensuring order in entrance and exit areas, while opening the way for original designs and variations, allowing the designer to create more original environments in architecture.
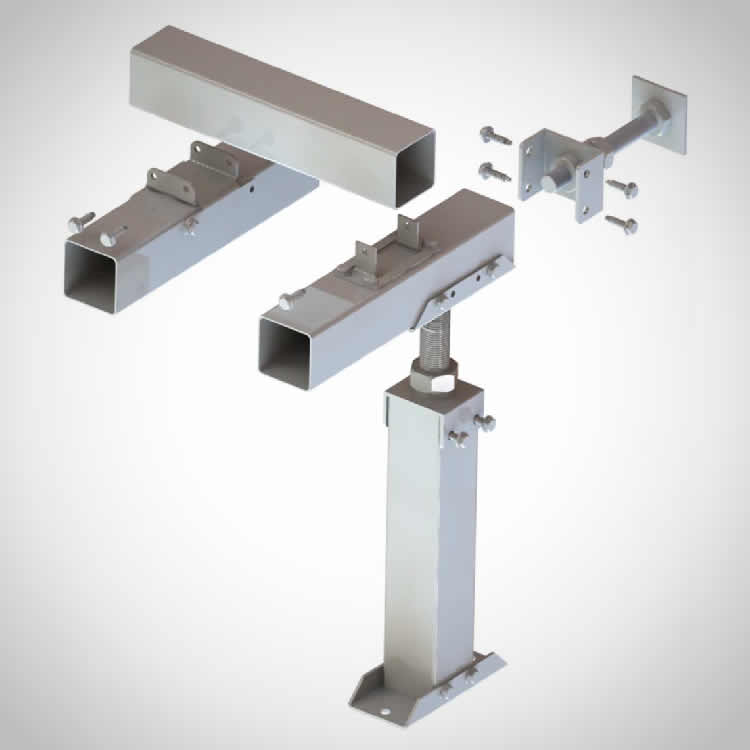
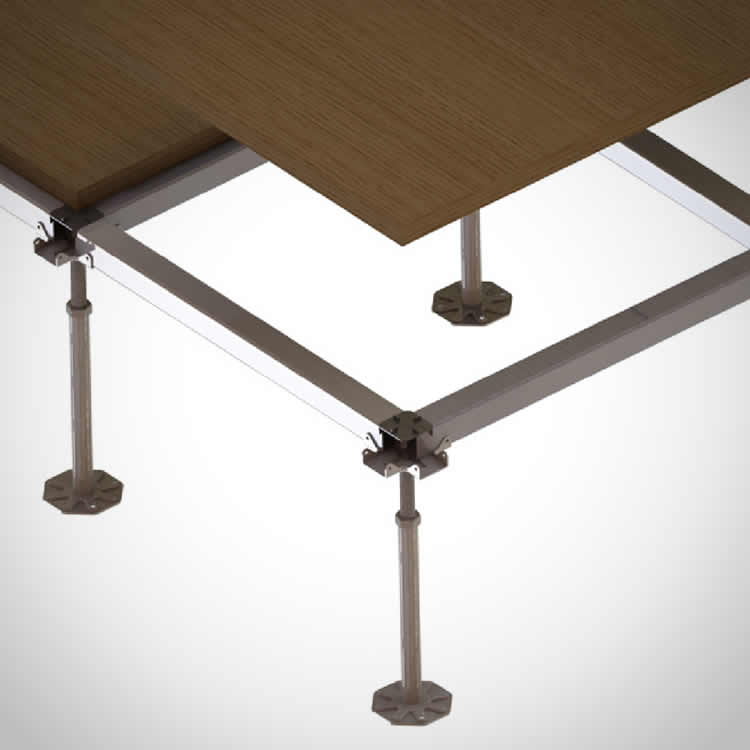
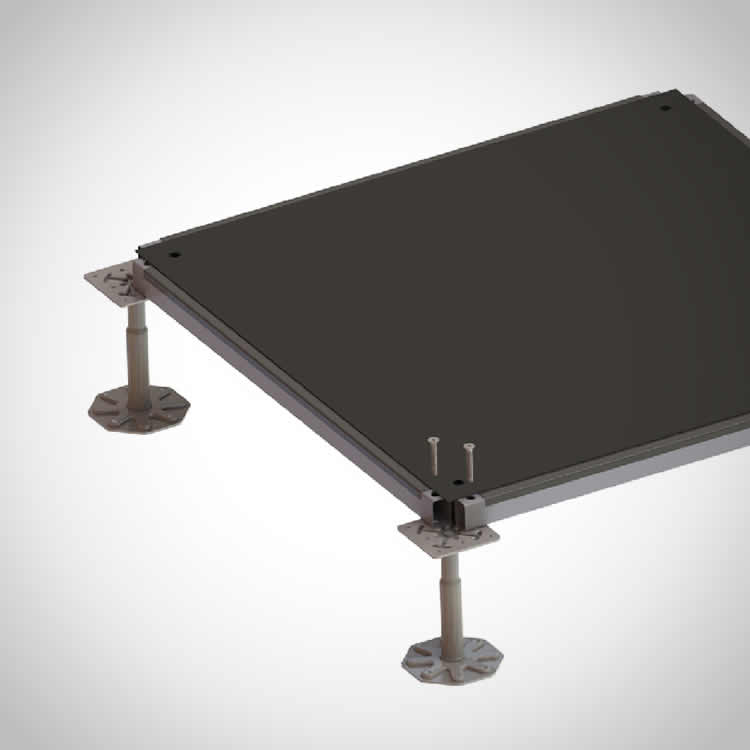
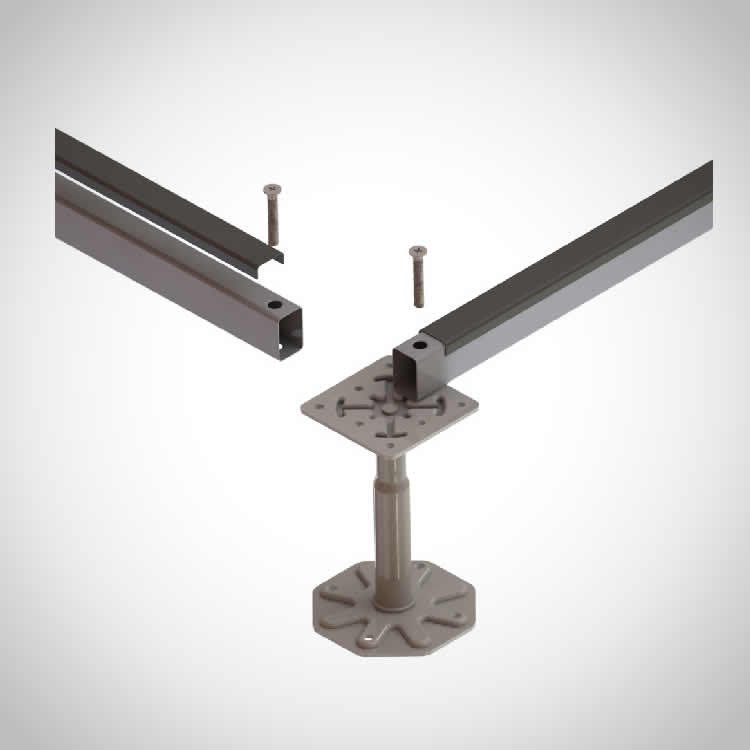
Technological devices that are now at our fingertips at every moment of our lives have radically changed our lifestyle and working methods. With the use of these devices, cable clutter and infrastructure problems have become inevitable.
Raised floorings eliminate this clutter by hiding all cables and installations under the floor and providing an aesthetic appearance.
Seismic floor systems are earthquake-resistant raised floor systems. They are used in areas where heavy loads are required.
Auco offers 3 different types of seismic flooring systems. Click here to view them in the products section. tıklayınız.
- Depending on the load, foot diameters of Ø21 – Ø25 mm or 40 x 40 mm square type can be used in seismic floor systems.
- Plastic strips are placed on the steel support cover for insulation. It has been developed for use with strips.
- There is a special fixing apparatus for fixing the steel feet to the wall in seismic floor systems.
Raised Access Floor Systems are modular and practical to apply. As a result of their practical application, they provide the necessary space for infrastructure installations and aim to facilitate intervention. Raised Access Floor Systems are highly preferred due to their practicality and affordability that allow you to shape your workspaces as you wish.
Standard Pedestal Feet For office type raised access floors, Basic system feet are used which do not have earthquake safety. As seen in the pictures in our company, there are 5 types of standard pedestal feet available.
Data centers, office floors, bank buildings, information processing centers, laboratories, shopping malls, universities, showrooms, exhibition areas, telephone switch centers, MSC centers, central control rooms and HV distribution rooms are the most common areas of use.
Raised floor systems offer freedom in open office decoration. They provide advantages in terms of cost, maintenance, and service in data centers, electrical and control rooms, and system rooms for cabling and labor. They eliminate static electricity problems and provide architectural design freedom. They also provide important air insulation for air conditioning and ventilation systems, leading to significant energy savings. Optional panel materials for raised floor surfaces include: steel sheet, concrete core, PVC, encapsulated, and wood.
- For the relevant load, pipe diameters of Ø21 – Ø25 mm or square type 40 x 40 mm can be used for the foot.
- The steel support cover is insulated with plastic strips. The strips are suitable for banded use.
**Standard Foot:** It is produced from a 21x1.5 pipe using an M14 stud for height adjustment. The head plate is 90x2.5 mm. The base plate is 90x2 mm. It is manufactured as galvanized metal. Metal feet, except for the minimum panel, are produced in various sizes starting from 2-3 heights up to 1500 mm. Before installation, the necessary elevation survey should be conducted in the environment, and the feet should be ordered in the appropriate size. AUCO provides all types of support to its customers before and after sales. 🛒🔧
In elevated floor infrastructure systems, the supports made of metal pipes used to keep the vertical carriers balanced, prevent them from toppling, collapsing, or sliding are called **braces**. For installations with a system height of 20 cm or more, we recommend using at least 1 brace per square meter. Different designs should be employed based on the system loads. 🏗️🔩📏
* Planning the Application : On the plan view of the area to be implemented, a 60x60 cm grid is laid out to draw the application plan. If accessories (such as ramps, steps, grilles, or skirting boards) will be used in the application, they should be included in the plan.
* Ground Preparation : If the floor to be implemented is rough or uneven, a screed application is necessary. If there is a sandy and easily breakable screed on the ground, a new screed application should be done. Materials such as moisture, water, chemicals, mud, etc., which could prevent the adhesive used to attach the load-bearing legs to the ground from adhering or cause it to come loose, should be cleaned or dried.
* Assembly Procedures : According to the grid plan, a center axis is created by pulling a chalk line at the specified dimensions. Starting from the center, the installation of the flooring panels begins, with the joints of the panels checked. The legs to be used in the application are brought to each corner of the panels and leveled. Since the foot position of each panel cannot be determined in advance, the panels are placed and adhered by positioning the legs. After all panels are mounted in this manner, the central part of the application area is completed, except for the edges. Pieces to be used along the wall edges are cut with an appropriate cutter and placed at the base of the walls. The panels are secured in place by compressing them using the plastic gaskets (plastic stars) on the legs, preventing movement.
YThe area where the Raised Flooring application will be carried out should be examined initially. The application area must be clean, with no concrete or screed residues on the floor.
* The dimensions of the area where Raised Flooring Installation will take place (due to the standard 60cm x 60cm panel dimensions) should be measured, and allowances for waste should be calculated.
* When calculating allowances, note that for the 60cm x 60cm raised flooring panels, if the dimensions do not exceed 30cm based on the wall measurements, two pieces can be obtained from one panel. However, for dimensions exceeding 30cm, the usability based on the remaining measurement should be assessed, considering the minimum waste. Panel and leg quantities should be determined accordingly.
* After creating the grid, to initiate the installation, a chalk line is pulled to establish the center axis according to the specified dimensions. Along the chalk line, the raised flooring panels are placed starting from the center, and for each panel placed, a raised flooring leg is brought to the corner and leveled. Once the assembly adjustments are made, the legs are either adhered to the floor using adhesive or fixed with dowels, depending on the situation. The foot locking nut is tightened.
* During the application, it is essential to avoid stepping on the raised flooring panels, as they are not designed to bear weight. Therefore, other ongoing work in the area should be temporarily halted or coordinated accordingly. The raised flooring system is modular, and it should not be stepped on from any side until it is fully secured on all four sides.
* Raised floor application cannot be applied independently of legs and panels.
The Raised Flooring System should not come into direct contact with water during both bottom and top cleaning. Alkaline or similar content detergents should not be used. Cilas used for surface protection and nourishment should not possess perfume and extra brightness features, as they may harm the upper surface.
Raised Floor Panels should always be wiped with a damp cloth that has been wrung out, avoiding direct contact with water. Abrasive paper, soda, or chlorine-containing substances should not be used. For Laminate-coated Raised Floor Panels, use cleaning cloths containing wool or wool content. For PVC-coated Raised Floor Panels, follow the maintenance instructions specified for the coated PVC surface.
Since carpet tiles are applied to Encapsulated Panels in the raised floor system, the maintenance requirements for the carpet apply. If a washable base has been used for the selected carpet, attention should be paid to the carpet joints, and water leakage should be prevented in these areas. In areas covered with this type of carpet, daily washing should be avoided, and the process should be carried out carefully at specific intervals. On Encapsulated Panels or foil-coated panels, abrasive materials, soda, chlorine-containing substances, and cleaning agents referred to as bleach should never be used on the surface.
We recommend using 0.5 mm galvanized steel as the underlayment for the raised floor panels, not aluminum foil. While plywood is a functional material, the purpose here is to prevent it from swelling due to exposure. However, aluminum foil can deform over time within the modular system, posing critical risks and potential costs in the near future.
In all system rooms, specifications are created with a uniform standard: 2mm heterogeneous PVC-coated panels. However, in critical system rooms and data center projects, especially in areas with high electrical intensity, conductivity is of utmost importance. Proper discharge of static electricity and effective grounding are crucial. Unfortunately, due to the absence of an organization that measures the conductivity of raised floor panels within the scope of the Turkish Standards Institute (TSE), it is not possible to measure the panels. Therefore, in all necessary areas, antistatic heterogeneous or homogeneous PVC-coated panels are used as the standard. However, it’s important to note that there is no conductivity between the upper PVC surface and the galvanized steel lower surface. Therefore, raised floor panels that cannot transfer this conductivity to the legs and grounding are employed.
In the raised flooring system, where we walk and occasionally intervene, the absence of static electricity discharge is of utmost importance within the area. It prevents significant costs and ensures the safety of devices and technical personnel. Electrostatic Discharge (ESD) plays a crucial role in such areas. It is specially manufactured and used based on measured values on-site. In the production of raised flooring that provides Electrostatic Discharge (ESD), the panels are not directly attached to metal parts or the upper surface. Instead, they are fed with conductive chemicals and covered with foil. The manufacturing process involves adhering homogeneous or heterogeneous PVC to the raised flooring panel. The lower surface of the panel is connected to galvanized steel, and copper strips are used on the infrastructure legs to ensure that static electricity is transmitted from the panel to the ground.